Well, I thought I’d keep up a thread as I work through a scratch build for my ESB Fett helmet. Full credit goes to Wizard Of Flight for the wonderful templates and Antman’s threads that really give some good advice, which you will see reflected in this build.
I started this project with a throw-away build using thin single thickness Crescent chipboard and paper (not shown here), just to see how everything goes together. I highly recommend this as I discovered sizing issues (such as fitting around my glasses) and details about the scaling of the PDFs with different printers, etc. In the end, 41% print scale for the helmet templates and 103% (on my Epson inkjet) for the dome template worked out for my sizing needs.
For the actual build, I’m using the double-thick Crescent chipboard. I've seen a few posts that suggest not using this because it is essentially two pieces of the thinner cardboard laminated together, but it is much more solid and actually has led to fewer issues for me thus far. I think it’s OK as long as you don’t keep moistening the same section of cardboard over and over again. Gorilla wood glue has really worked out well for me as well.
Wrapping the inner portion and clamping in place:
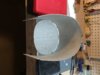
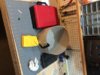
Because of how I clamped the back side, I ended up with a slight curvature on the back of my bucket between the top and the bottom. To correct this, I moistened the area and clamped for a few hours with narrow wood to correct this. I did not let it go full dry because I didn't want the bucket to get totally flat on the back:
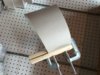
I clamped the sides using 2” boards on the range finder side and 1 and 3/4" on the other side and let it fully dry to get it nice and flat (note: wood that is laminated worked best lest you end up with wood grain pressed into the cardboard):
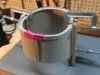
I started this project with a throw-away build using thin single thickness Crescent chipboard and paper (not shown here), just to see how everything goes together. I highly recommend this as I discovered sizing issues (such as fitting around my glasses) and details about the scaling of the PDFs with different printers, etc. In the end, 41% print scale for the helmet templates and 103% (on my Epson inkjet) for the dome template worked out for my sizing needs.
For the actual build, I’m using the double-thick Crescent chipboard. I've seen a few posts that suggest not using this because it is essentially two pieces of the thinner cardboard laminated together, but it is much more solid and actually has led to fewer issues for me thus far. I think it’s OK as long as you don’t keep moistening the same section of cardboard over and over again. Gorilla wood glue has really worked out well for me as well.
Wrapping the inner portion and clamping in place:
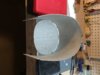
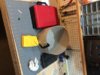
Because of how I clamped the back side, I ended up with a slight curvature on the back of my bucket between the top and the bottom. To correct this, I moistened the area and clamped for a few hours with narrow wood to correct this. I did not let it go full dry because I didn't want the bucket to get totally flat on the back:
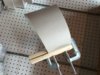
I clamped the sides using 2” boards on the range finder side and 1 and 3/4" on the other side and let it fully dry to get it nice and flat (note: wood that is laminated worked best lest you end up with wood grain pressed into the cardboard):
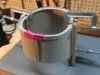
Last edited by a moderator: