Also, some more lil updates. Got the final red layer on the rear keyholes done, also the killstripes.
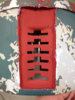
The old grey that was on there from the original painting of that area was a little rough textured, so I steel wooled it a bit. Doing so made the layers spot through each other a little more than I like though, but it's probably not worth the bother and risk of messing things up to try to micro-mask and repaint them. This is intended to be a pretty economy paint-up, so a few smaller issues like that are ok as long as the general aesthetic isn't hurt.
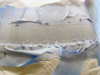
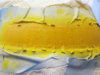
The killstripes were a challenge to get masked up. I ended up getting a little two stripe template card made up which made things easier.
The white layer was a primer layer as I didn't want to have to do 100 layers of yellow to keep the green from showing through. For the yellow/orange gradient I tried to keep it pretty subtle, as it seems that way in most references. I'm pretty sure for the actual original prop they only used 1 color for the stripes, and the gradient comes from how thickly they painted it over the green, but it's a challenge to replicate an effect like that without knowing the exact colors and weathering they used. Also, I'm still a pretty inexperienced painter, so simple is better.
There's a few chips of bright yellow showing through the orange, due to me de-masking the stripes before the orange layer had dried and bonded properly. Not really any way to fix them unfortunatly as that's now a unique mixed orange/yellow shade that I'll never be able to approximate. Bob Ross would call it a happy accident though, as it fits alright with the chipped damage theme.
Another little thing I did was give a metallic effect to my Borden connector.
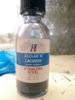
Since the Borden is supposed to be an actual metal piece that gets glued in, I didn't want it to just use the same fakey looking Silver 11 the rest of the helmet has. So to make it look distinct like it does in the references, I painted it with some Alclad II metallic lacquer, which gives some very realistic effects. The picture doesn't give it too much justice, as it has quite a realistic sheen in person.